One of the first things you learn as a welder is that you should first ground whatever you’re grounding. If you don’t ground it correctly, some issues could arise, and your equipment would suffer in the long run.
However, a common problem most welders face is where to ground when welding on a car. Luckily, we have the answers for you. By the end of this article, you’ll get a much clearer idea about where to ground when welding on a car; let’s get started.
Is It OK to Weld on a Vehicle?
Yes, welding on a vehicle is OK. Many people weld on a car for many reasons. Some include repairing damaged metals, reinforcing structural parts, and creating custom parts. While welding on a car, it’s essential to take the proper precautions, which means having the necessary equipment and skills to perform the weld correctly.
Before welding on a vehicle, you should remove all flammable materials from the scene, like gasoline and fuel. Also, provide ample protection for sensitive electrical systems and component. This is important because welding generates sparks, UV light, and intense heat.
Therefore, you should wear eye protection, a welding mask, and protective clothing.
You also need a clear understanding of the type of metal you’re welding because some metals, like magnesium and aluminum, need special welding equipment and techniques. If you’re a new welder, it’s always best to ask for the assistance of a professional when welding on a vehicle.
Where Should I Ground My Car When Welding?
When welding your car, you’ll need a place to ground the metal. It’s essential to choose a safe location. This is to prevent electrical hazards and ensure proper metal grounding when welding. The best option to ground the metal is the frame or chassis of the car.
This location will ensure a direct, low-resistance path to the battery’s negative terminal. It will also prevent any form of electrical arcing.
When you’re grounding the metal, ensure you attach the clamp of the welding machine to a clean metal surface of the car’s frame or chassis. Your location should also be free of rust, paint, or other insulations affecting its electrical conductivity.
We also recommend keeping the cable as short as possible; this will reduce any form of resistance. Also, keep the ground cable away from hot surfaces or moving parts.
What Happens If You Don’t Ground a Welder?
Welding can be very dangerous, but you can avoid potential injuries like electric shocks and burns with the right information. To prevent electric shocks, grounding is essential. If you don’t ground a welder, it could result in electrical hazards and poor weld quality.
When welding, an electrical current passes through the metal, creating a circuit between the welded metal and the welder.
Without grounding the metal, the electrical current arcs, and this causes sparks to begin jumping from the metal to other surfaces. If the spark falls on the welder’s body or inflammable material, it could result in electric shock or fire.
In addition to electrical shock or fire, not grounding the metal can also cause poor-quality welds. This is because grounding the metal creates a low-resistance path for the electric current to follow. This ensures proper heating for the welding process.
The metal won’t be properly heated without grounding the welding, resulting in weak or porous welds. To avoid such issues, it’s always best to ground the welder in a safe location.
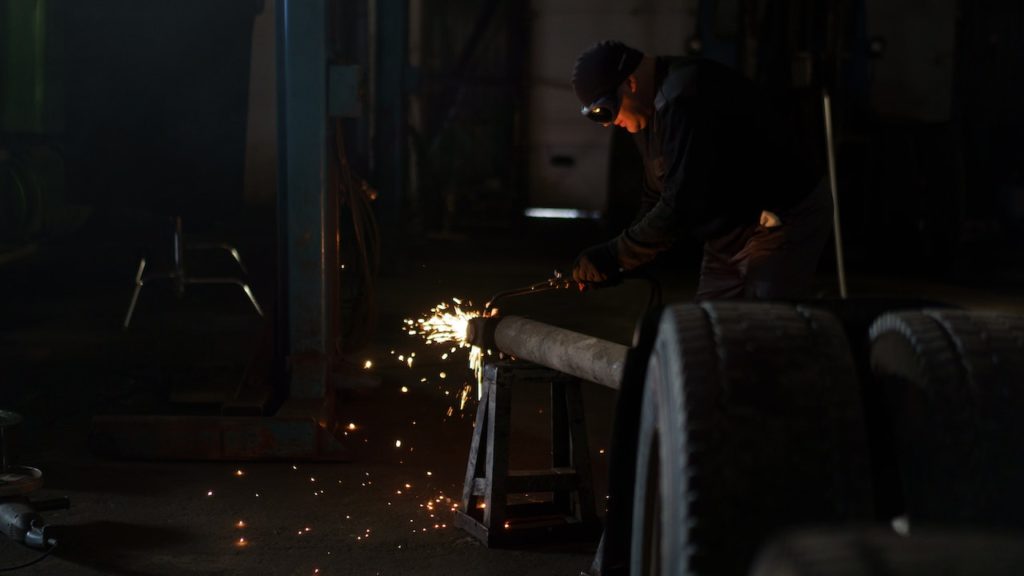
Where Does the Ground Clamp Go When Welding?
A welder needs to know where to put the ground clamps when welding. You should always attach the clamp to the vehicle you’re welding. The closer the ground clamp is to where you’re welding, the better the quality of your welds.
It’s crucial to remember that you should always place the clamp on clean material. This means materials covered in paint or rusty are not the best option. If possible, sand a part of the metal to ensure it is clean before you place your clamp on it. This ensures a good connection for the welding process.
If you’re welding on a vehicle, the best option is disconnecting the battery before you begin welding. Additionally, avoid clamping directly to the wheels, as this could damage the wheel bearing. The best choice for welding on a car is MIG welding because it is quite safe.
Do You Have to Disconnect the Battery When Welding on a Vehicle?
It’s generally recommended to disconnect the battery when welding on a vehicle. This ensures no damage to the sensitive electrical components and minimizes the risk of electrical hazards.
The welding process generates UV light, intense heat, and sparks which could damage the car’s electrical system like spark plugs and alternators.
When you disconnect the batter, it prevents all forms of risks to this part by removing the source of electrical current and breaking the electrical circuit when welding.
Additionally, removing the battery significantly reduces the risk of electrical shock or fire caused by sparks during the welding process.
While welding, an electrical current passes through the metal being welded. This creates a circuit between the welder and the metal. If you don’t disconnect the battery, the electrical current will flow through the car’s electrical system, resulting in electrical arcs or sparks.
If you want to remove the battery, first remove the negative cable from the battery’s negative terminal. This is the best approach for batteries located under the hood. However, if the batter can be found in the trunk, removing the positive cable is best.
Additionally, keep the battery and its cables away from hot surfaces or sparks that could occur during the welding process.
Conclusion
After reading this article, you’ll have a clearer idea of the importance of grounding when welding on a car and the best location to ground during the welding process. A top-quality grounding clamp will improve your weld’s quality and make welding on a vehicle much easier. The fewer things going wrong, the easier it will be to concentrate on getting the weld right.
Add comment